In machining, hole machining accounts for about 1/3 of the total machining. Hole machining is semi-enclosed cutting. Chip removal, heat transfer, cutting liquid cooling are all difficult, especially more difficult hole deep processing.
The classification of the hole:
- 1) by shape: there are cylindrical holes, conical holes, drum holes, polygonal holes, spline holes and other special-shaped holes (such as curved holes), etc. Among them, cylindrical holes are most widely used.
- 2) by form: there are through-hole and blind hole (blocked hole); Deep hole (L/D = 5 ~ 20 is a general deep hole, L/D is a medium deep hole, L/D is a medium deep hole, and L/D﹥30 ~ 100 is called a special deep hole) and a shallow hole.
- 3) according to the size of aperture: there are big holes (D﹥100mm), ordinary holes (D = 10~100mm), small holes (D=1~10mm) and micro holes (D < 1mm).
- 4) according to the processing mechanism: mechanical processing, special processing, electromechanical compound machining, etc. Although there are many special machining methods, the traditional machining will still be the main method of hole machining because of the expensive equipment and low processing efficiency.
- 5) according to the machining accuracy: Rough machining holes (such as holes after boring and rough boring), semi-fine bore (such as reaming, coarse ream, semi-fine boring hole) and precise hole (such as fine hinge, fine pull, fine grinding, honing, grinding hole). Precision holes generally refer to tolerances above grade IT7 – IT6 and surface roughness is Ra﹤ 0.8~0.4m. Its geometrical shape precision (such as roundness, cylindrical degree, axis straightness, etc.) is generally specified in the range of 1/2 ~ 1/3 of its dimensional tolerance band.
With the rapid development of aerospace, automobile, high-speed train, wind power, electronics, household appliances, energy, mold, hydraulic, machine tool and precision machinery and other equipment manufacturing industries and the upgrading of products, the application of precision holes is increasing day by day.
Characteristics of hole machining:
Hole machining is a complex process, which must solve the problem of chip removal, cooling, lubrication and guidance. Hole machining has a wide range of applications. The quality of its processing will directly affect the use and life of the product. The cutting mechanism of hole machining is complex, the cutting tools are various, and the machining is difficult. In mechanical parts, the precision and surface roughness of the hole are required to be improved day by day. Precision hole machining is often the key to production. In order to improve the economic efficiency of hole processing, many factories use advanced cutting tools: polygonal rotary broaching tools, single blade boring reamer of cemented carbide, precision diamond burnishing tools or cubic boron nitride reamer, roller burnishing tools and other new processes.
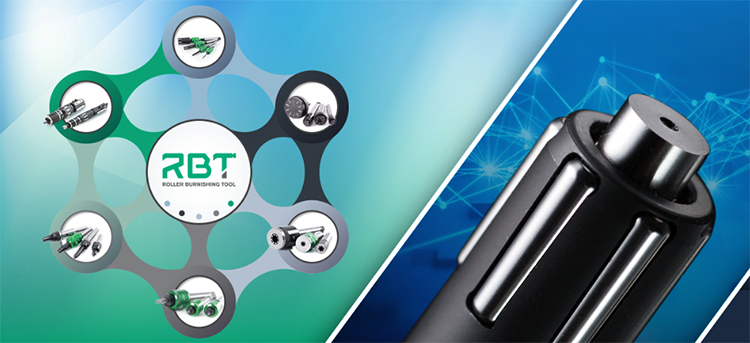
roller burnishing tools, skiving burnishing tools, rotary broaching tools, deburring and chamfering tools, external roller burnishing machines manufacturer
RBT is the one-stop solution provider for burnishing hole. Our burnishing tools covers roller burnishing tools, skiving burnishing tools, rotary broaching tools, deburring and chamfering tools, external roller burnishing machines, etc. Since the company was founded in 2007, we have served over 2,000 customers worldwide. Welcome new and old customers come to the consultation to discuss!